Investment: SMIR Magnetic Overhead Crane
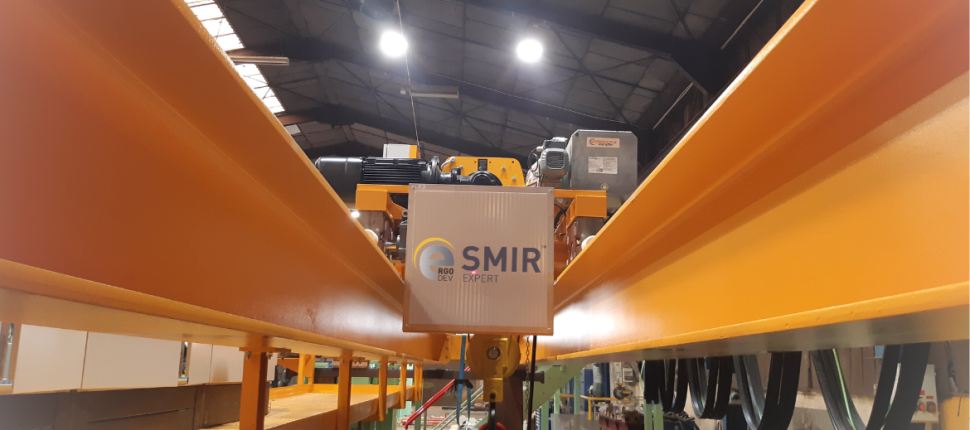
The automated crane will use a magnet to pick up bulk material and deposit it in a defined location. The stockpile is made up of fixed locations selected by the operator for depositing.
The system is designed for a production rate of:
- Operating time 3 x 8 over 5 days, with an output of 160 tons over 16 hours per day.
- Minimum 13 cycles of 800 kg per hour.
- The magnet is unhooked and hooked by the operator.
Setting up a Magnetic Overhead Crane
In the foundry world, efficiency and safety are top priorities. The constant search for innovative technologies to improve manufacturing processes has led to the introduction of a revolutionary solution: the magnet bridge. This emerging technology offers significant advantages in terms of heavy load handling and productivity. In this article, we explore the ins and outs of implementing a magnet bridge in a foundry.
What is a magnet crane?
A magnet bridge, also known as a magnetic bridge or magnetic crane, is a lifting system that uses powerful magnets to lift and move heavy metal loads. Unlike traditional cranes, which use hooks or tongs, a magnet crane can grasp materials safely and effectively thanks to magnetic force.
Advantages of using a magnet crane:
- Increased lifting capacity: Magnet crane are capable of lifting much heavier loads than traditional lifting equipment, enabling large and heavy parts to be handled with ease.
- Improved safety: Thanks to their ability to hold loads in place through magnetic force, magnet cranes reduce the risk of falls and accidents associated with traditional lifting methods, ensuring a safer working environment for employees.
- Time-saving: The speed and efficiency with which loads can be lifted speeds up material handling operations, resulting in increased productivity and reduced downtime.
- Versatility: A wide variety of ferrous materials can be handled, including bars and castings, making it a versatile tool for foundry operations.
Old magnet crane


Dismantling the old magnet crane

Receipt of the new SMIR Magnetic Overhead Crane


Delivery / Installation
